Anechoic Chambers : Evolution of the Anechoic Chamber Industry over the last 20 years and its future
11/19/2024
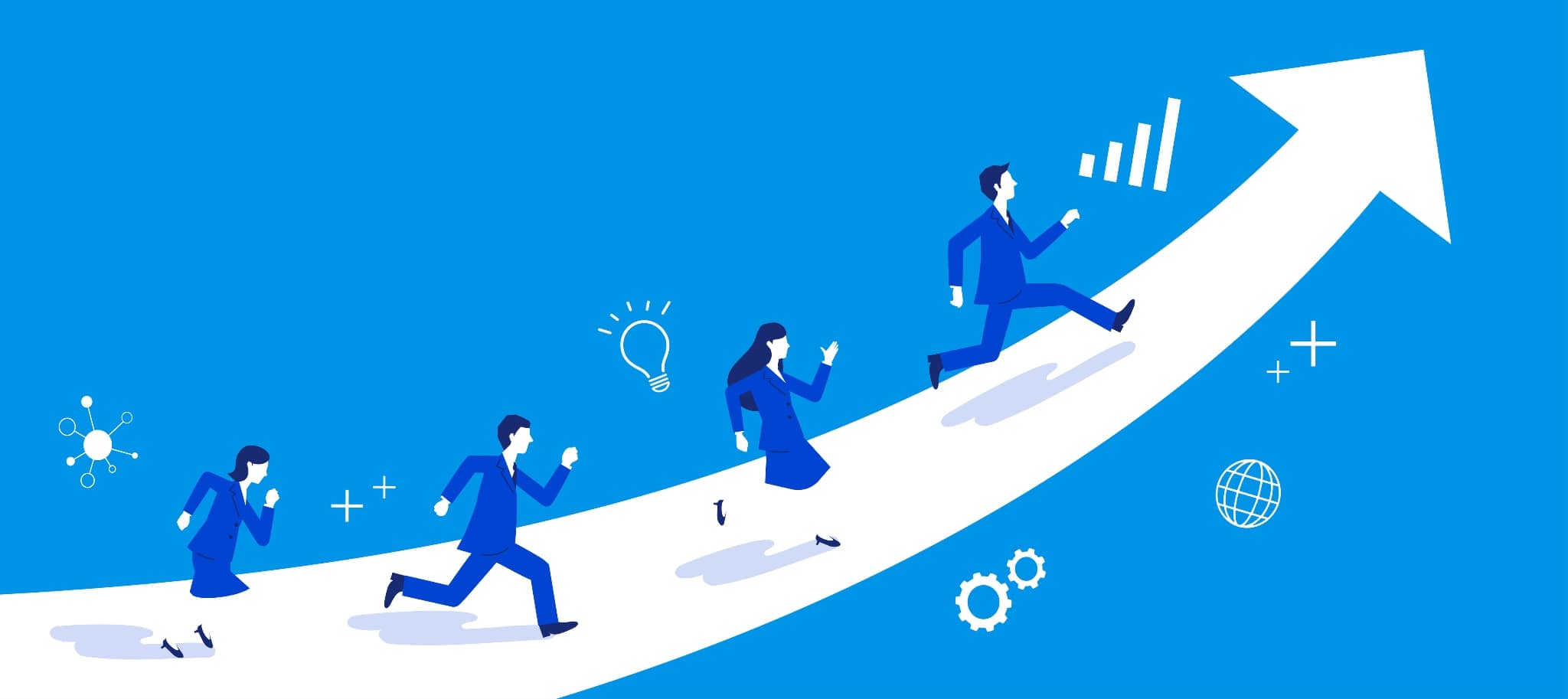
MFAC / MSAC
We would like to discuss how anechoic chambers and the anechoic chamber industry have changed from 2003, the year our company, Sonora Technology, was established to the present.
Around 2003 The mainstream was anechoic chamber built using standard construction methods
When our company was established, we focused primarily on noise control solutions and were a new entrant in the anechoic chamber industry when we first ventured into it.
At that time, anechoic chambers were extremely expensive, costing nearly 1.5 to 3 times what they do today.
The typical construction of anechoic chambers was as follows. We refer to this as the “Showa specification” in our company, as it has not changed since the Showa era.
Soundproofing Layer | Concrete + Air |
Sound-absorbing layer | Glass wool 32K + Wire frame + cordura fabric |
Around 2004 The emergence of modular panel anechoic chambers
When our company began developing and selling anechoic chambers, we decided to create chambers using steel, which is our area of expertise. As mentioned earlier, this was not a typical construction method, and there was skepticism in the industry about whether it could truly be used for anechoic chambers. However, after continuing development and conducting verification tests from the previous year, we successfully commercialized modular anechoic chambers.
Our company delivered its first anechoic chamber in March 2004 to Apex ADS Company (which appears to be out of business now.) Unlike today, the soundproof panels had a double structure, and the walls were quite thick and heavy.
That same year, our company published a lineup of anechoic chamber specifications and set prices close to a level that disrupted the market. In some bidding cases, the bid prices for anechoic chambers from other companies were twice as high as ours.
Around this time, one of the largest anechoic chambers in Japan was constructed by Company K. (Unfortunately, we were able to secure the order.)
Around 2005 Expansion of the sales of modular anechoic chambers
Our company expanded the sales of modular anechoic chambers, building a track record of deliveries to automotive manufacturers, home appliance makers, and more. Additionally, we continuously improved soundproof panels and sound-absorbing wedges each year, promoting thinner and lighter designs.
As a new entrant in the industry offering affordable and unconventional anechoic chambers, our company was likely viewed with disdain by some in the field. We even encountered critical comments on certain forums.
At that time, there were still many anechoic chamber manufacturers (about nine companies) in existence. Our company, along with its affiliates, was the only one to publicly announce standard prices for anechoic chambers. This has not changed to this day. We believed that anechoic chambers were too expensive and that a fair pricing adjustment was necessary.
Around 2007 Construction of modular anechoic chambers overseas
We delivered our first anechoic chamber for export to Company T in the Philippines.
Since modular anechoic chambers are literally a combination of parts, they were well-suited for export. In the following year, we also constructed an anechoic chamber in the United States.
Around this time, the revenue from anechoic chamber- related sales exceeded half of our total sales.
Around 2008 Development of temperature-controlled anechoic chambers
We developed a temperature and humidity-controlled anechoic chamber with an insulation layer and special air conditioning equipment. This enabled us to conduct complex tests under specific temperature conditions using the anechoic chamber.
Around 2009 Establishment of our factory and research and development base
The establishment of the Fujisan Technical Center in Gotemba City, Shizuoka Prefecture, served as a significant turning point for us. This led to accelerated development progress and enabled us to achieve further thinning and lightweight of the soundproof and sound-absorbing layers.
There are now about four major anechoic chamber manufacturers, including our company. While some manufactures have gradually been eliminated over time, I believe this is because those companies have continued to follow specifications that have not changed since the Showa era and have neglected new technology development.
We exhibited our anechoic chambers at the Automotive Testing Expo in Germany.
During this event, we exchanged information with various overseas anechoic chamber manufacturers, which led to the emergence of new development themes.
Around 2010 Development of flat-silence soundproof doors
The flat sill is a special door structure that does not have a threshold at the bottom. It can be used even in anechoic chambers that require high soundproofing performance.
This design emerged from the increasing awareness of safety within companies.
Around 2012 Revision of ISO 3745
The significant revision of ISO 3745, which serves as the standard for measurement and design methods for anechoic chambers, brought about major changes in the nature of anechoic chambers. Not only in Japan, but also overseas, anechoic chamber manufacturers began to emerge, and this revision sparked an increased demand for anechoic chambers.
~Around 2020 A new era of anechoic chambers
While there is now little competition domestically, we increasingly found ourselves competing with three major companies overseas. Domestic manufacturers that could not meeting the new standards struggled to expand their sales both in Japan and abroad.
Additionally, issues such as a shortage of skilled engineers became apparent, leading to the closure of several anechoic chamber manufacturers.
Around 2022 Orders for anechoic chambers in the UK
Until now, our overseas orders has been almost exclusively from Japanese companies, but we received an order for an anechoic chamber from a major electrical manufacturer in the UK.
Around 2023 Development of the new sound-absorbing wedge BFW
Starting in 2020, we developed a sound-absorbing material using DuPontʼs Tyvek as part of the BF series and released the new sound-absorbing wedge, BFW.
Around 2024 Commencement of full-scale overseas sales
Due to the increasing global demand for semi-anechoic chambers for automotive acoustic testing (VSAC), we launched our global website and officially started overseas sales.
~Present Summary
I believe 2012 marked a significant turning point for anechoic chambers. Prior to that, the manufacturing costs of the old-type sound-absorbing wedges, which followed the Showa specifications, has been rising in Japan ( due to a decline in companies processing wire for the wedge shapes), creating a challenging situation.
Those who have read this far may have one question : Why were domestic anechoic chamber manufacturers unable to create new anechoic chambers ?
I believe there are two main reasons for this.
- (1) Anechoic chambers were not a main product, so development budgets were not allocated for them.
- (2) They were unable to perceive changes in the anechoic chamber industry and shifts in user needs.
In summary, I have discussed the evolution of anechoic chambers from the time of our companyʼs establishment to the present. Looking back, I can see that the design methods for anechoic chambers, the surrounding industry environment, and the increase in overseas demand have all changed significantly.
As a specialized manufacturer, our company will continue to promote forward-looking development and contribute to the advancement of the industry.